What Is a Pneumatic Control Valve?
The main function of a pneumatic control valve (also known as a directional control valve or pneumatic valve) is to switch airflow. It uses compressed air to control the flow, pressure, or direction of a fluid (gas or liquid) within a pneumatic system. These valves act as final control elements in many automation and process systems, enabling precise regulation based on input signals or manual operation.
There are numerous categories and a wide variety of pneumatic valves. They can be classified by their style, type, design principle, mode of operation, function, size, and application. They can also be distinguished by their actuation method, such as manual, mechanical, hydraulic, or pneumatic.
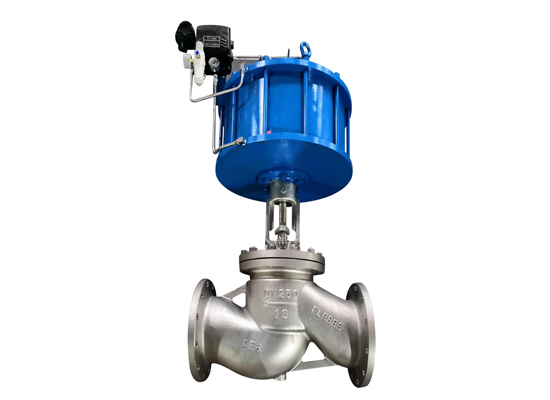
What is pneumatics?
Pneumatics involve using compressed air to produce mechanical motion. This technology plays a vital role in operating control valves and finds widespread use across multiple industries. Beyond automation, pneumatics is also applied in fields like dentistry, construction, and mining. In all these cases, air serves as the primary energy source for pneumatic systems.
Working Principle Explained
Pneumatic valves are automatic fluid control valves that do not directly rely on the fluid's own pressure or movement.The control process of a pneumatic control valve primarily operates through the interaction of the controller, positioner, and actuator.
First, the controller continuously monitors process variables such as temperature, pressure, and flow according to operational requirements, and sends a control signal to the positioner. The positioner acts as a bridge between the controller and the actuator. It receives the control signal and simultaneously detects whether the current valve position matches the target position. If there is any deviation, the positioner adjusts the air pressure output to the actuator for real-time correction.The actuator then responds to the air pressure from the positioner by moving the valve stem up and down or rotating it, thereby adjusting the valve opening to precisely regulate the flow of the medium.
This coordinated process enables the pneumatic control valve to perform fast, stable, and controllable automated operations. As a result, it is widely used in industrial process control, HVAC systems, energy, manufacturing, and other fields.
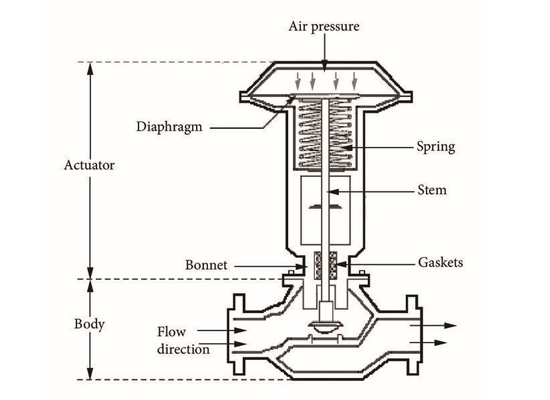
Types of Pneumatic Valves
A pneumatic valve is an automatic control valve that is operated by an external actuator using compressed air as the driving force to open, close, or regulate the valve, can be configured in various ways, including:
Based on the number of possible flow paths or switching positions
According to the number of inlet and outlet ports
By the mechanism used to open or close the ports
Depending on the valve’s default (non-actuated) state
Pneumatic control valves come in a wide range of types and are used to control or completely block airflow. They are essential for connecting or disconnecting the main compressed air supply in pneumatic systems, and for operating actuators such as cylinders that perform extension and retraction movements.
Common types include:
Two-way pneumatic control valves
Three-way directional control pneumatic valves
Four-way directional control pneumatic valves
Spring-return (spring-biased) pneumatic valves
A pneumatic valve is an automatic control valve that is operated by an external actuator using compressed air as the driving force to open, close, or regulate the valve.Different structures and functions of pneumatic valves are suited for different application fields:
Two-way, two-position valve
This valve has two ports and two positions, used to simply allow or block airflow. It is commonly used for switching air sources on or off.
Three-way, two-position valve
With three ports and two positions, this valve switches between supply and exhaust. It is typically used to control the extension and return of single-acting cylinders.
Four-way, two-position valve
Featuring four ports and two positions, it controls double-acting cylinders to perform motion in two directions.
Four-way, three-position valve
This valve also has four ports but three positions. The center position can be configured as closed, exhaust, or pressurized, offering various mid-position functions such as hold, release, or lock when controlling double-acting cylinders.
Spring-return pneumatic valves
These valves automatically return to their initial position when no control signal is present, enhancing system safety and auto-reset capability. They are widely used in scenarios requiring fail-safe position holding or automatic reset upon power loss.
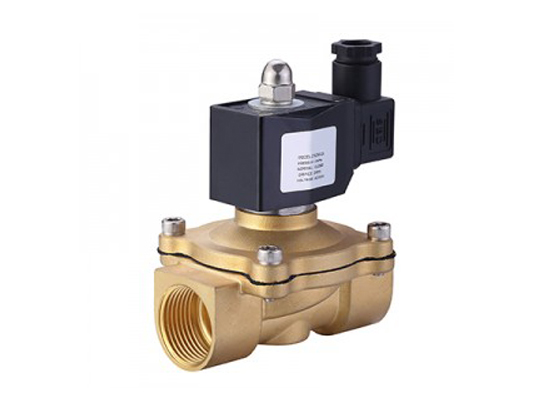
Pneumatic Valve Types Based on Actuator
Pneumatic valves can be classified based on their actuator type, including manual, pneumatic, solenoid, and electric actuators. Common types include:
Manual pneumatic valves: Operated by handles, knobs, or foot pedals, these valves have a simple structure and are suitable for applications with low operating frequency.
Air-piloted pneumatic valves: Controlled by compressed air signals, they drive the valve spool to switch positions. These are commonly used in remote control or automated systems due to their fast response and high reliability.
Solenoid pneumatic valves: Actuated by an energized solenoid, they switch the valve spool position and are the most common control method in automated systems. They are ideal for high-frequency, fast switching operations.
Electric pneumatic valves: Driven by electric actuators such as servo motors, these valves are suitable for applications requiring precise adjustment of valve position.
Additionally, spring-return valves are often used in combination with pneumatic or solenoid controls. They automatically return to their initial position when the control signal is lost, providing fail-safe operation or power-loss protection.
Different types of actuators are selected based on application requirements and are widely used across various industrial automation control systems.
Pneumatic valve VS Solenoid valve
Pneumatic valves and solenoid valves are both types of automatic fluid control valves that do not directly rely on the fluid’s own pressure or movement. Below are the specific differences in their structure, function, and applications:
Pneumatic Valves
Driven by compressed air to operate actuators; can achieve complex control logic through manual operation, electro-pneumatic control, PLC, etc.; fast response; relatively complex in structure and requires air source and actuators for operation and maintenance; under the action of a positioner, it can achieve high-precision control and is suitable for regulation; robust structure with long service life; widely used in automated production lines, cylinder control, large-scale process control, and precision regulation applications.
Solenoid Valves
Use electromagnetic force to directly drive the valve core; primarily controlled by on/off electrical signals to open or close the valve; extremely fast response, ideal for high-frequency switching; typically used for on/off control with limited adjustment capability; simple structure, easy to install and maintain, but electronic components are susceptible to high temperatures and humidity. Widely used in household appliances, water treatment systems, sprinkler systems, and small fluid control systems.
Advantages of Pneumatic Systems
Pneumatic systems are designed to use compressed air to transmit and control energy. In various fields such as food processing, pharmaceuticals, and automated production lines, pneumatic technology is often the driving force behind operations.
Fast Response and High Sensitivity
Compressed air flows at high speed, enabling actuators (such as cylinders) to start and stop quickly. In precision electronic assembly, such as for chips and PCB boards, pneumatic grippers and push rods can perform high-frequency operations like picking, placing, and aligning components within milliseconds, greatly improving cycle efficiency.
Simple Structure and Easy Maintenance
A pneumatic system is composed mainly of cylinders, valves, and pipelines. It has a relatively simple structure, is easy to maintain, features high interchangeability of parts, and is convenient to install and replace.
High Safety
Compressed air is used as the working medium, which eliminates the risk of sparks and explosions. Even if leakage occurs, it does not pollute the environment or pose harm to personnel.
Strong Environmental Adaptability
Pneumatic systems can operate normally in harsh environments such as humidity, dust, high temperature, and vibration. They are easy to disassemble and highly flexible.